Maximizing Efficiency and Reliability with Advanced Downhole Filters in Drilling Operations
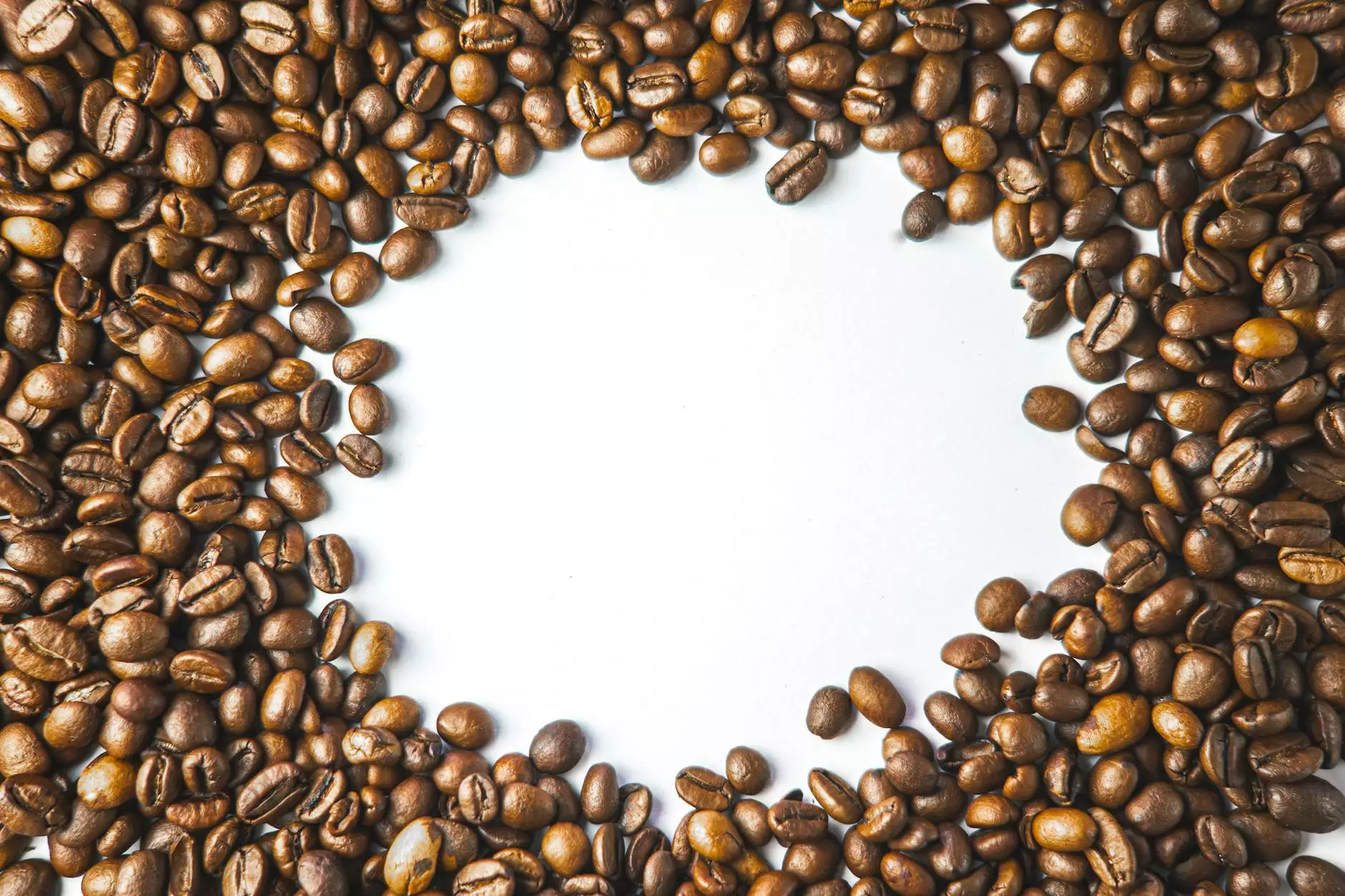
In the highly competitive and technologically demanding world of oil and gas exploration, efficient drilling operations are paramount to success. Central to this efficiency are high-quality downhole filters, which serve as critical components in maintaining the integrity of drilling fluids, protecting drill equipment, and ensuring environmental safety. As industry leaders in Building Supplies and Machine & Tool Rental, maverick-drilling.com underscores the importance of cutting-edge downhole filters for modern drilling projects.
Understanding the Role of Downhole Filters in the Drilling Ecosystem
Downhole filters are specialized filtration devices installed down the wellbore to remove unwanted particles, debris, and impurities from drilling fluids. Their primary function is to safeguard the drill string, prevent clogging, and maintain optimal fluid properties. Effective filtration directly impacts the rate of penetration, formation integrity, and overall operational safety.
Typically, these filters are engineered from robust materials capable of withstanding extreme pressures, corrosive environments, and high temperatures encountered during drilling. They come in various designs, including screen filters, disc filters, and composite filtration systems, each tailored to specific operational needs.
The Critical Importance of Downhole Filters in Modern Drilling
1. Enhancing Drilling Efficiency
- Reduced Drill Pipe Sticking: Clean drilling fluids free of debris minimize stuck pipe incidents, saving time and operational costs.
- Optimized Drilling Speed: Proper filtration ensures smooth fluid flow, enabling faster penetration rates.
- Minimized Equipment Wear and Tear: Removing abrasive particles prolongs the lifespan of drill bits and downhole tools.
2. Improving Wellbore Stability and Formation Protection
- Prevention of Formation Damage: By filtering out particles that could invade formation interfaces.
- Maintaining Proper Hydrostatic Pressure: Consistent fluid quality prevents lost circulation and blowout risks.
3. Environmental Safety and Regulatory Compliance
- Reducing Environmental Impact: Efficient filtration prevents contaminated fluids from leaking into surrounding formations.
- Meeting Industry Standards: Compliance with environmental regulations is facilitated by high-performance downhole filtration systems.
Innovations in Downhole Filter Technology
Recent advancements in downhole filtration technology have revolutionized how drilling operations are conducted. These innovations focus on increasing filtration efficiency, durability, and adaptability to specific well conditions.
Advanced Materials
- Nanomaterial Coatings: Enable filters to trap smaller particles with higher precision while resisting corrosion.
- Composite Materials: Combine strength and flexibility, allowing filters to withstand high-pressure environments without degradation.
Modular and Customizable Designs
- Tailored Filtration Systems: Customized filters designed for specific well geometries and fluid properties.
- Easy Installation and Maintenance: Modular units facilitate quick replacements and minimal operational disruption.
Smart Filtration Solutions
- Integrated Sensors: Monitor filter performance in real-time, alerting operators to potential clogging or failure.
- Data Analytics: Use collected data to optimize drilling parameters and predict maintenance needs.
Choosing the Right Downhole Filter for Your Drilling Needs
Selecting the appropriate downhole filter is a nuanced process that depends on various operational parameters, including well depth, formation type, fluid composition, and environmental conditions. Key factors to consider include:
Filtration Capacity and Particle Retention
Ensuring the filter can trap the size and amount of debris expected in the specific drilling environment is critical. High filtration capacity prevents clogging and maintains steady fluid flow.
Compatibility with Drilling Fluids
Filters must be compatible with various drilling fluids, whether water-based, oil-based, or synthetic. Material choice and design influence this compatibility.
Durability and Resistance
Extreme pressures, temperature fluctuations, and corrosive substances require filters made from robust materials that can perform reliably over extended periods.
Ease of Deployment and Removal
Designs that facilitate quick installation, inspection, and replacement minimize downtime and operational costs.
Implementing Best Practices for Optimal Downhole Filter Performance
To maximize the benefits of downhole filters, organizations should adhere to best practices including:
- Regular Monitoring and Maintenance: Use smart sensors and data analytics to track filter performance and initiate preventive maintenance.
- Training of Personnel: Ensure that drilling crews are proficient in installing, inspecting, and replacing filters efficiently.
- Quality Assurance: Source filters from reputable manufacturers with proven track records of durability and performance.
- Customized Solutions: Collaborate with filtration specialists to design systems tailored to unique well profiles and operational goals.
The Future of Downhole Filters in the Drilling Industry
The evolution of downhole filters is driven by innovations in materials science, automation, and data integration. Future trends include:
- Artificial Intelligence Integration: Enhancing predictive maintenance and real-time performance analysis.
- Enhanced Material Durability: Developing even more resistant components capable of withstanding harsher environments.
- Environmental Sustainability: Designing eco-friendly filters that minimize waste and environmental impact.
- Adaptive Filtration Systems: Dynamic filters that adjust their filtration capacity based on real-time well conditions.
Why Choose Maverick Drilling for Your Downhole Filtration Needs?
At maverick-drilling.com, we are committed to providing top-tier building supplies and reliable machine & tool rental services tailored to the drilling industry. Our extensive product range includes cutting-edge downhole filters engineered to meet the highest industry standards. With our expertise, you benefit from:
- Premium Quality Products: Ensuring reliability and longevity in your drilling projects.
- Customized Solutions: Addressing specific operational challenges with tailored filtration systems.
- Technical Support and Consultation: Expert guidance to optimize your filtration setup and overall drilling performance.
- Fast Delivery and Turnaround: Minimizing downtime and maintaining project schedules efficiently.
Conclusion: The Strategic Value of Downhole Filters in Modern Drilling
In today's complex drilling environments, effective downhole filtration is not just a maintenance task but a strategic element that significantly influences operational success. Investing in advanced downhole filters ensures cleaner drilling fluids, reduced equipment wear, enhanced safety, and many other benefits that drive cost savings and productivity. As industry standards evolve and environmental considerations become ever more critical, innovative filtration solutions like those offered by maverick-drilling.com are essential for staying ahead in the competitive landscape.
Choosing the right filtration system empowers your drilling operations to operate more smoothly, with fewer interruptions, and with greater confidence in environmental stewardship. Whether you are undertaking small-scale exploratory drilling or large infrastructural projects, ensuring robust downhole filtration is a fundamental step toward achieving your operational goals.
Harness the power of state-of-the-art downhole filters today and propel your drilling projects toward greater efficiency, safety, and sustainability.